Best practices for industrial temperature management include regular calibration of sensors, maintaining optimal ranges, and implementing robust monitoring systems for safety and efficiency.
Proper temperature management is critical for industrial operations. From manufacturing plants to chemical processing, maintaining precise temperatures ensures product quality, equipment longevity, and energy efficiency. This guide covers essential best practices for industrial temperature control.
Temperature Measurement Installation
Accurate temperature monitoring begins with proper sensor installation. Key considerations include:
Thermowell Installation
- Position in locations that reflect true process temperatures
- Ensure accessibility for maintenance
- Verify material compatibility with process media
- Choose appropriate connection type (threaded, welded, or flanged)
For optimal performance, consider precise thermostat controls to complement your sensor network.
Sensor Placement
Sensors must contact the thermowell bottom for accurate readings. Proper insertion depth prevents measurement errors from thermal gradients.
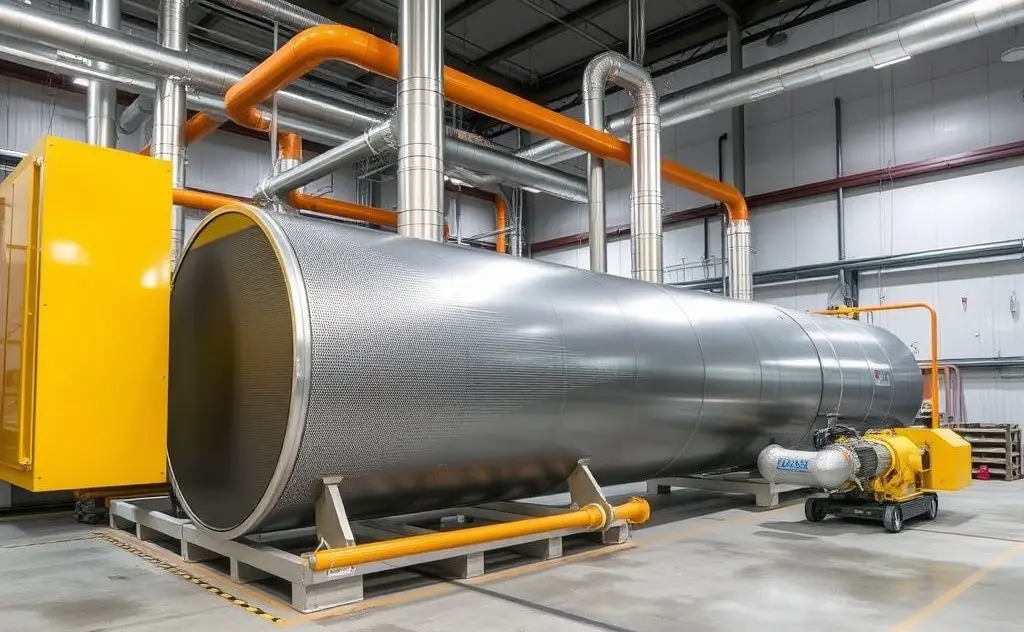
Heat Recovery Strategies
Industrial processes generate significant waste heat that can be repurposed. According to the Compressed Air & Gas Institute, 96% of electrical energy in air compressors converts to recoverable heat.
Effective Heat Recovery Methods
Application | Temperature Range | Potential Uses |
---|---|---|
Screw Compressors | Up to 300°F | Space heating, process water |
Oil-less Systems | Higher than 300°F | Combustion air pre-heating |
Implementation Tips
- Use ducting to channel warm air to needed areas
- Install thermostatic controls for automatic regulation
- Consider industrial blower systems for heat distribution
System Maintenance & Optimization
Regular Calibration
Schedule periodic sensor calibration to maintain measurement accuracy. Document all calibration activities for quality control.
Grounding Practices
Proper grounding prevents electromagnetic interference. Follow facility guidelines for:
- Shield grounding at sensor housing
- DCS ground connections
- Transmitter isolation when required
Energy Efficiency Measures
The U.S. Department of Energy recommends these strategies for industrial temperature systems:
Insulation Improvements
- Upgrade pipe insulation to current standards
- Seal leaks in ductwork and enclosures
- Consider advanced heating elements for better thermal transfer
Process Optimization
- Match temperature setpoints to actual process needs
- Implement staged heating where possible
- Use variable speed drives on circulation pumps
Safety Considerations
High-Temperature Protocols
- Install redundant temperature cutoffs
- Maintain clear access to emergency shutoffs
- Use appropriate personal protective equipment
Hazardous Area Installations
In explosive environments, use intrinsically safe equipment and follow NEC/CEC classification requirements.