Temperature significantly influences adhesive performance by affecting the viscosity, curing time, and bonding strength; higher temperatures can accelerate curing but may reduce adhesion in some materials, while lower temperatures can slow curing and potentially lead to incomplete bonding or brittleness.
Temperature dramatically affects how adhesives bond, cure, and maintain strength over time. Whether you’re using industrial epoxies or household tapes, understanding thermal effects ensures reliable results. This guide explores temperature’s role in adhesion with practical solutions for extreme conditions.
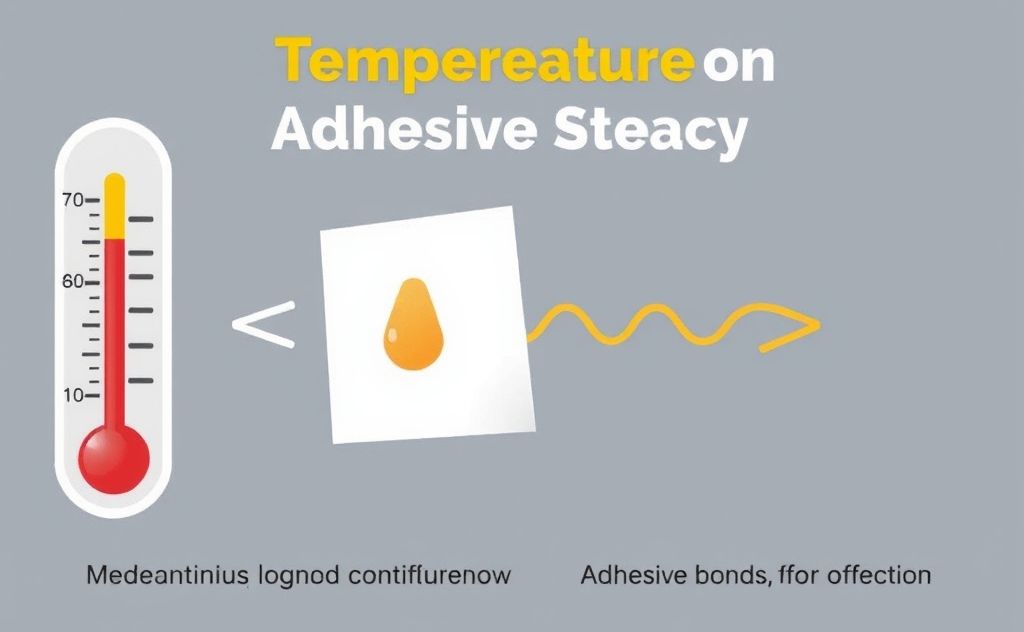
Why Temperature Matters for Adhesives
Adhesives rely on molecular interactions that change with temperature. Heat accelerates chemical reactions while cold slows them. Most adhesives perform best between 60-80°F (15-27°C). Outside this range, bonds may weaken or fail prematurely. Cold temperatures affect materials differently than heat, requiring specific adhesive formulations.
Ideal Temperature Ranges by Adhesive Type
Adhesive Type | Minimum Temp | Optimal Range | Maximum Temp |
---|---|---|---|
Cyanoacrylate (Super Glue) | 40°F (4°C) | 70-80°F (21-27°C) | 180°F (82°C) |
Epoxy | 50°F (10°C) | 65-90°F (18-32°C) | 300°F (149°C) |
Hot Melt | 250°F (121°C) | 350-400°F (177-204°C) | 450°F (232°C) |
Pressure-Sensitive Tape | 32°F (0°C) | 60-80°F (15-27°C) | 150°F (66°C) |
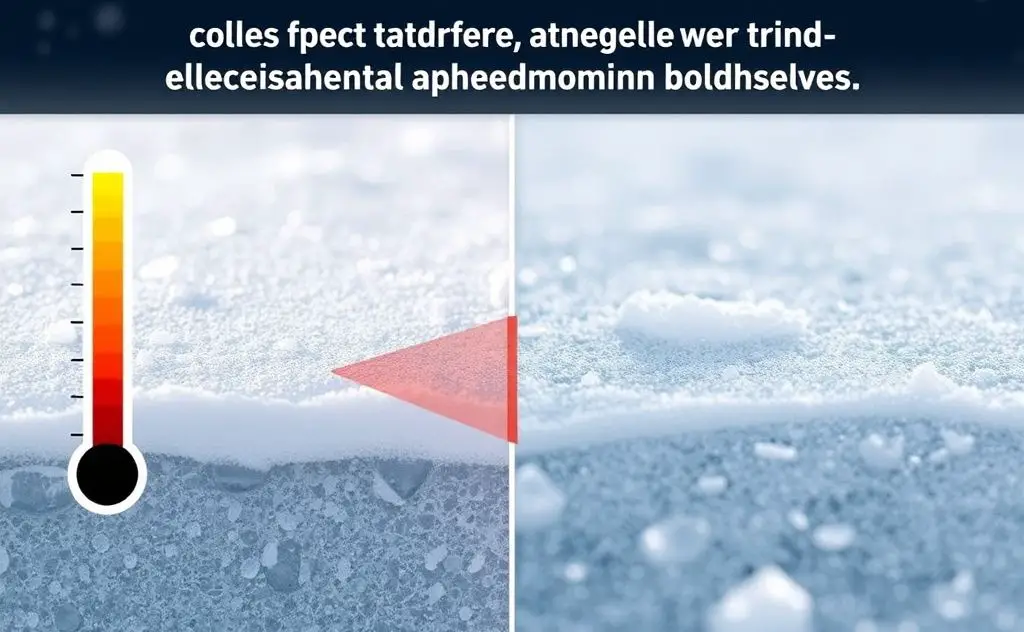
Cold Temperature Effects on Adhesives
Low temperatures cause multiple adhesive performance issues:
1. Reduced Tack & Wetting Ability
Cold makes adhesives stiffer, preventing proper surface contact. A ASTM study showed tape adhesion drops 30% at 40°F compared to room temperature.
2. Brittle Bonds
Polymer chains lose flexibility in cold, making bonds prone to cracking under stress. This is especially problematic for plastics and composites that contract in cold.
3. Slower Curing Times
Chemical reactions slow dramatically in cold. Some epoxies may take 3-4x longer to cure at 50°F versus 70°F.
Cold Weather Solutions:
- Pre-warm substrates with heat guns or space heaters
- Use winter-grade formulations with plasticizers
- Allow 50% longer cure times below 60°F
High Temperature Effects on Adhesives
Excessive heat causes different failure modes:
1. Softening & Creep
Adhesives may become viscous above their glass transition temperature, allowing bonded parts to slip.
2. Thermal Degradation
Prolonged heat exposure breaks polymer chains. Silicones typically withstand 400°F+ while acrylics fail above 250°F.
3. Outgassing
Volatile components evaporate, leaving brittle residues. This is critical in sealed electronics applications.
Heat Resistance Solutions:
- Choose high-temp adhesives (epoxies > silicones > acrylics)
- Use mechanical fasteners as backups
- Implement thermal barriers or heat sinks
Temperature Cycling Challenges
Repeated heating/cooling causes:
- Differential expansion between materials
- Fatigue cracks at bond lines
- Adhesive embrittlement over time
Automotive underhood applications may see -40°F to 300°F cycles. Specialty adhesives with flexible fillers perform best in these conditions.
Best Practices for Temperature Management
Storage Conditions
Store adhesives at 50-77°F (10-25°C) in climate-controlled areas. Avoid garages or sheds with extreme temperature swings.
Application Techniques
For cold environments:
- Warm substrates to at least 60°F before bonding
- Use portable heaters to maintain temperature during cure
For hot environments:
- Apply adhesives during cooler morning hours
- Use fast-cure formulations to minimize heat exposure
Material Selection Guide
Temperature Range | Recommended Adhesives |
---|---|
-100°F to +250°F (-73°C to 121°C) | Modified epoxies, polyurethanes |
-60°F to +400°F (-51°C to 204°C) | Silicones, high-temp epoxies |
-320°F to +500°F (-196°C to 260°C) | Ceramic-filled adhesives |
Proper adhesive selection and temperature control ensures durable bonds in any environment. For extreme conditions, consult adhesive manufacturers for specialized formulations.