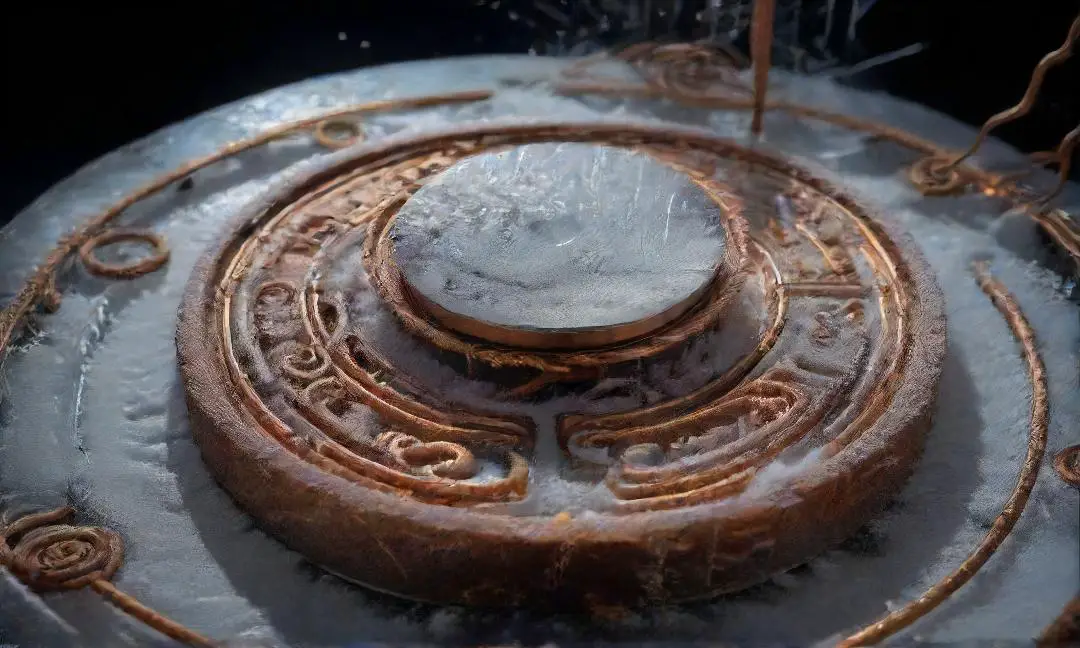
The Chilling Truth: How Cold Impacts Metals
Cold Temperature’s Impact on Metal Properties
Cold temperatures can significantly alter the properties of metals, causing them to become more brittle and prone to fracturing. This change in behavior is due to the contraction of metal molecules in the cold, leading to reduced flexibility and increased susceptibility to stress.
Common Metal Reactions in Cold Environments
When exposed to cold environments, metals may undergo various reactions such as thermal contraction, which can result in dimensional changes and structural stress. Additionally, certain metals may experience corrosion or oxidation when subjected to prolonged cold conditions.
Preventing Cold-Related Metal Damage
To prevent damage caused by cold temperatures, it is essential to implement proper insulation and heating mechanisms for metal components. Regular maintenance and monitoring can help detect early signs of cold-induced damage and allow for timely intervention to mitigate further deterioration.
Choosing the Right Metals for Cold Conditions
Selecting appropriate metals for applications in cold environments is crucial to ensure optimal performance and longevity. Metals with high resistance to low temperatures, such as stainless steel or aluminum alloys, are preferred choices for cold-weather applications to minimize the risk of failure.
Case Studies: Real-World Examples of Cold-Induced Metal Failures
Examining real-world case studies of cold-induced metal failures provides valuable insights into the consequences of inadequate metal selection or insufficient cold-weather protection measures. By learning from past failures, engineers and designers can enrich their absorbing of cold-related metal challenges and improve future decision-making processes.
Frosty Foes: Uncovering the Science Behind Metal Fractures in Cold
Assimilating Brittle Fracture in Metals
Metal materials, when subjected to extreme cold, can undergo a phenomenon known as brittle fracture. This occurs when the metal loses its ductility and becomes prone to sudden and catastrophic failure without warning.
Factors Contributing to Cold-Induced Fractures
Cold-induced fractures in metals can be influenced by various factors such as the material composition, the rate of temperature change, and the presence of residual stresses. These elements can interact in complex ways, making it crucial to understand their combined effects.
Testing Methods for Assessing Metal Resilience in Cold
Metallurgical engineers employ advanced testing methods to assess the resilience of metals in cold environments. Techniques like Charpy impact testing and ultrasonic testing provide valuable insights into the material’s ability to withstand cold-induced stresses.
Strategies for Mitigating Fracture Risks in Cold Environments
To mitigate fracture risks in cold environments, engineers often resort to preheating, post-weld heat treatment, and the selection of appropriate materials with enhanced cold resistance. These strategies help intensify the metal’s toughness and reduce the likelihood of fractures.
Expert Insights: Tips from Metallurgical Engineers on Cold Fracture Prevention
Metallurgical engineers emphasize the importance of proactive measures to prevent cold-induced fractures in metals. They recommend regular inspections, monitoring of temperature fluctuations, and the implementation of preventive maintenance practices to safeguard against potential failures.
Cold Conundrum: How Temperature Variations Affect Metal Structures
Thermal Expansion and Contraction in Metals: Metals are not immune to the whims of temperature. When the mercury drops, metals contract, causing them to shrink and potentially impacting their structural integrity. Conversely, as temperatures rise, metals expand, posing a different set of challenges.
Implications of Temperature Fluctuations on Metal Integrity: The constant battle between hot and cold can lead to metal fatigue, cracks, and even failure. Discerning how temperature variations affect metal properties is crucial for preventing costly repairs and ensuring the longevity of metal structures.
Structural Design Considerations for Cold-Prone Areas: In regions where frigid temperatures reign supreme, architects and engineers must carefully consider the impact of cold on metal structures. Factors such as material selection, joint design, and load-bearing capacity play a pivotal role in safeguarding against the detrimental effects of extreme cold.
Insulation Techniques to Regulate Metal Temperatures: To combat the chilling effects of cold weather on metals, insulation emerges as a hero. By insulating metal structures, thermal conductivity is reduced, helping to maintain optimal temperatures and prevent unwanted fluctuations that could compromise structural stability.
Balancing Strength and Flexibility: Optimizing Metal Performance in Changing Climates: Achieving the perfect balance between strength and flexibility is paramount relating to metal performance in fluctuating climates. Metals must be robust enough to withstand external forces meanwhile remaining flexible to accommodate temperature-induced expansions and contractions.
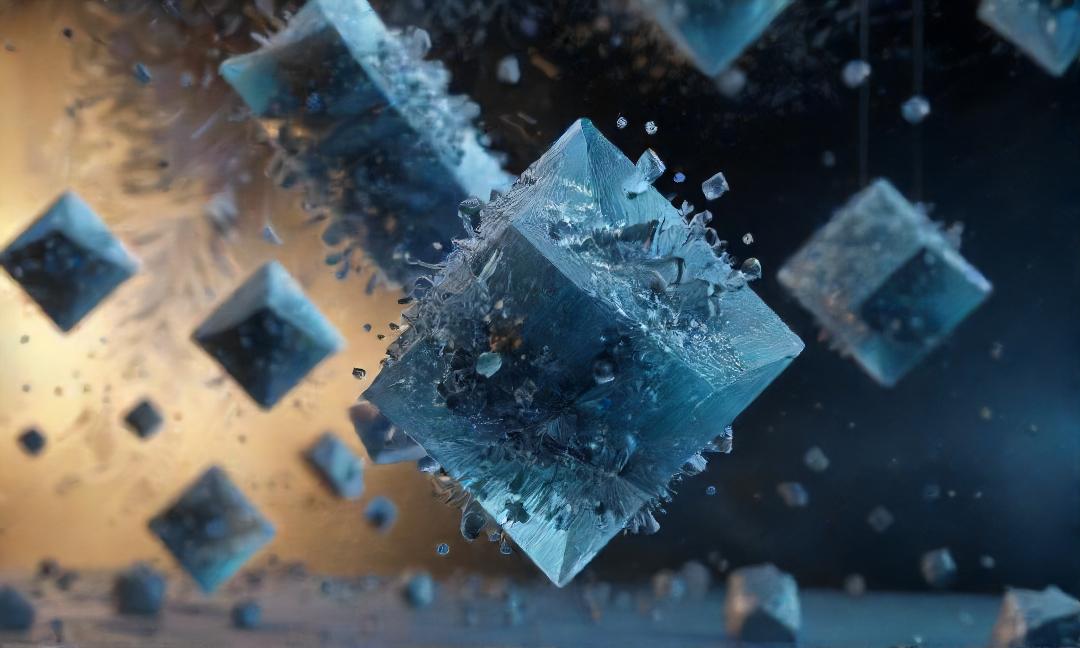
Freezing Facts: The Relationship Between Cold and Corrosion in Metals
Corrosion Mechanisms Triggered by Cold Conditions
When temperatures plummet, metals face a formidable foe in the form of corrosion. Cold conditions accelerate the chemical reactions that cause metals to deteriorate, leading to increased vulnerability to rust and degradation. The chilling effect of cold on metals can expedite the breakdown process, making it crucial to understand and combat these corrosion mechanisms promptly.
Corrosion Prevention Methods for Cold-Exposed Metals
Shielding metals from the harsh impact of cold environments requires proactive measures. Implementing corrosion prevention methods such as galvanization, sacrificial anode installation, and cathodic protection can fortify metal surfaces against the detrimental effects of low temperatures. By employing these strategies, metal structures can maintain their integrity and longevity even in freezing conditions.
Impact of Moisture and Salts on Cold-Induced Corrosion
Moisture and salts act as catalysts for corrosion, particularly in cold climates. When metals are exposed to freezing temperatures combined with moisture and salt deposits, the corrosion process intensifies. This potent combination accelerates metal degradation, emphasizing the critical role of moisture and salts in exacerbating cold-induced corrosion.
Protective Coatings and Treatments for Cold-Prone Metal Surfaces
To combat the corrosive effects of cold on metals, protective coatings and treatments play a pivotal role. Applying specialized coatings such as epoxy, polyurethane, or thermal spray can create a barrier that shields metal surfaces from cold-induced corrosion. These protective measures serve as a defense mechanism, safeguarding metals from the detrimental impact of low temperatures.
Sustainability Practices: Eco-Friendly Corrosion Solutions for Cold Environments
In the quest for environmentally conscious corrosion solutions, sustainable practices offer a promising avenue for combating cold-induced corrosion. Utilizing eco-friendly coatings, corrosion inhibitors derived from natural sources, and renewable treatments can provide effective protection for metals in cold environments meanwhile minimizing the ecological footprint. Embracing sustainability practices ensures that metal preservation aligns with environmental responsibility, fostering a harmonious relationship between cold conditions and corrosion prevention.
Icy Insights: Navigating Cold-Weather Challenges in Metal Maintenance
Best Practices for Winterizing Metal Equipment
Winter brings its own set of challenges for metal equipment. To ensure longevity and optimal performance, it’s crucial to implement effective winterization practices. Insulating vulnerable parts and applying protective coatings can shield metal equipment from the harsh cold.
Dealing with Ice Accumulation on Metal Surfaces
Ice buildup on metal surfaces can be a major headache during winter. Employing de-icing methods such as gentle heating or using specialized ice melt products can help prevent damage and maintain the integrity of the metal surfaces.
Lubrication Tips for Cold-Weather Metal Machinery
Cold weather can cause lubricants to thicken, affecting the smooth operation of metal machinery. Opt for cold-weather lubricants that remain fluid in low temperatures to ensure proper lubrication and prevent wear and tear on metal components.
Emergency Repair Protocols for Cold-Related Metal Failures
When faced with sudden metal failures due to extreme cold, having emergency repair protocols in place is essential. Quick response times, access to spare parts, and skilled technicians can help minimize downtime and swiftly address cold-related metal failures.
User-Friendly Maintenance Guides for Cold-Exposed Metal Assets
Maintaining metal assets exposed to cold weather requires regular upkeep. User-friendly maintenance guides can provide step-by-step instructions on inspecting, cleaning, and protecting metal assets, empowering users to proactively care for their equipment.
What are effects of cold on metals
Cold temperatures can have significant effects on metals, including increased brittleness, reduced flexibility, and potential corrosion. Discerning these effects is crucial for implementing proactive maintenance strategies to mitigate the impact of cold weather on metal assets.
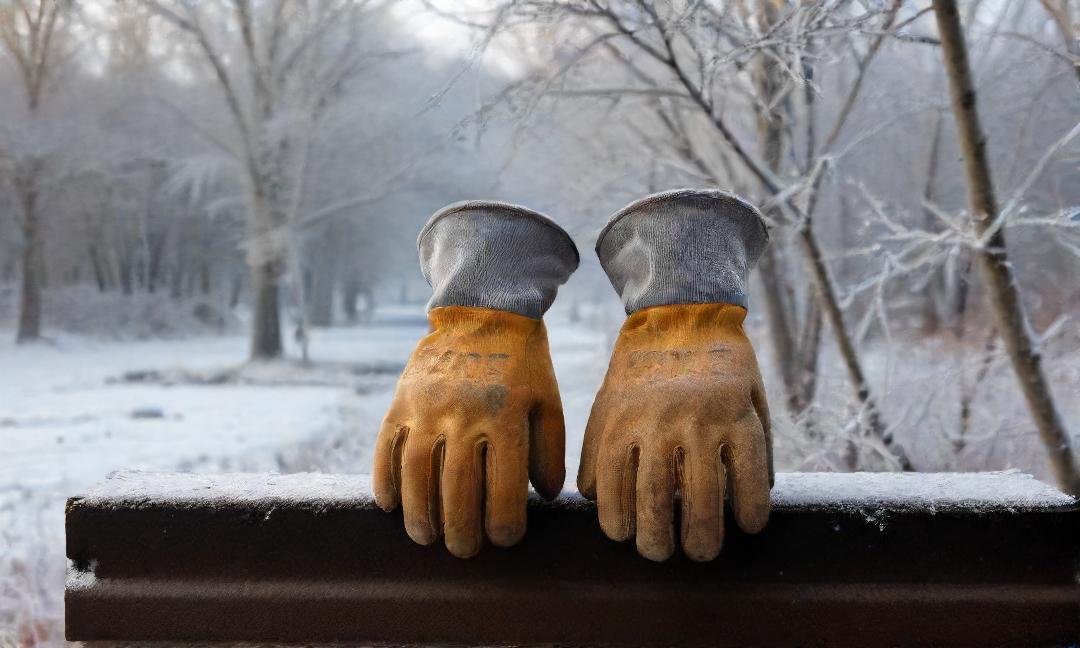
Frostbite or Fortitude: How Metals Adapt to Extreme Cold Conditions
1. Metallurgical Innovations for Cold-Resistant Alloys
Metallurgical wizards have concocted a symphony of elements to forge alloys that scoff at the biting cold. Through a meticulous dance of chemistry and craftsmanship, these alloys emerge as the unsung heroes of freezing environments, standing strong against the icy grip of winter.
2. Cold-Weather Testing Standards for Metal Durability
In the realm of metal durability, cold-weather testing sets the stage for a showdown between the elements and the resilience of metals. These standards are the battlegrounds where metals prove their mettle, enduring frigid temperatures with unwavering fortitude.
3. Advancements in Cryogenic Metal Applications
Cryogenic metal applications have unlocked a realm of possibilities, pushing the boundaries of what metals can endure in extreme cold. From space exploration to medical marvels, these advancements showcase the adaptability and versatility of metals in the harshest of conditions.
4. Future Trends in Cold-Weather Metal Engineering
The crystal ball of cold-weather metal engineering reveals a future filled with innovation and resilience. As technology marches forward, so too do the capabilities of metals in withstanding the frosty embrace of winter, promising a horizon of endless possibilities.
5. Adapting to the Chill: Strategies for Enhancing Metal Performance in Extreme Cold
When the cold winds howl, metal performance must rise to the occasion. Strategies abound for enhancing the fortitude of metals in extreme cold, from insulation techniques to structural reinforcements, ensuring that frostbite remains a distant threat in the world of metal mastery.