Compressors in heat pump HVAC systems are essential components that circulate refrigerant, compressing it to increase its pressure and temperature, thereby enabling efficient heat transfer for heating or cooling indoor spaces.
The compressor is the heart of any heat pump HVAC system. This critical component circulates refrigerant and enables heat transfer between indoor and outdoor environments. Understanding compressor operation helps homeowners maintain systems and choose efficient models.
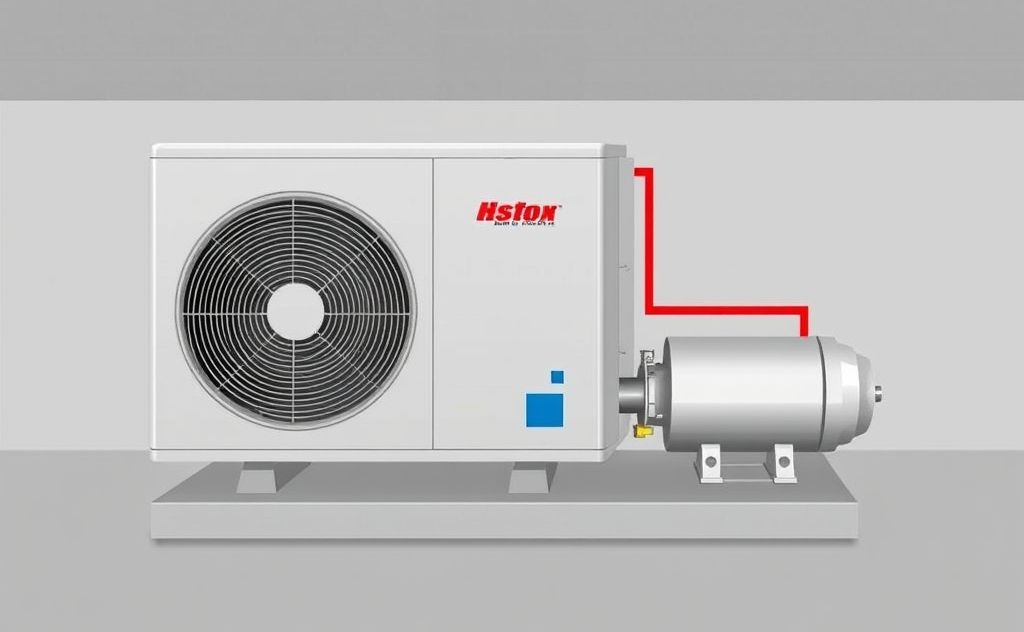
What Does a Compressor Do in a Heat Pump?
Heat pump compressors have three key functions:
- Pressurizes refrigerant gas to enable heat absorption/release
- Circulates refrigerant through the closed-loop system
- Maintains proper refrigerant flow rates for optimal performance
Unlike convection heating systems, heat pumps don’t generate heat. They move thermal energy using refrigerant and compressor technology.
Compressor Types in Modern Heat Pumps
1. Reciprocating Compressors
Piston-driven workhorses found in older systems. Reliable but less efficient than newer designs.
2. Scroll Compressors
Spiral components compress refrigerant with fewer moving parts. Common in mid-range systems.
3. Rotary Compressors
Use rotating vanes for smooth operation. Compact and quiet but less durable.
4. Inverter Compressors
Variable-speed operation matches output to demand. Most efficient option available today.
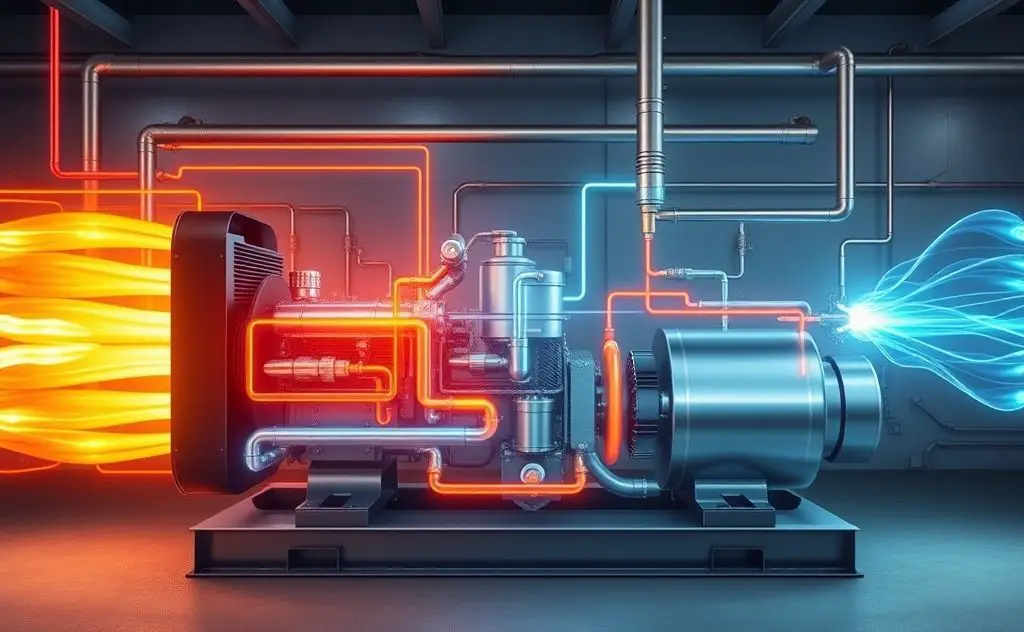
How Compressors Enable Heating and Cooling
The compressor enables the refrigerant cycle that makes heat pumps unique:
Mode | Compressor Action | Heat Transfer |
---|---|---|
Heating | Compresses cold refrigerant vapor | Absorbs outdoor heat, releases indoors |
Cooling | Compresses warm refrigerant vapor | Absorbs indoor heat, releases outdoors |
This reversible operation is why heat pumps outperform traditional electric heating systems in efficiency.
Advanced Compressor Technologies
Modern innovations improve compressor performance:
- Two-stage compressors: Operate at 65% or 100% capacity for better efficiency
- Variable-speed compressors: Adjust output in 1% increments for precise temperature control
- Oil-free compressors: Eliminate lubrication needs for reduced maintenance
According to U.S. Department of Energy, inverter-driven compressors can reduce energy use by 30-50% compared to single-speed models.
Compressor Maintenance and Troubleshooting
Proper care extends compressor life:
Preventative Maintenance
- Clean outdoor coils annually
- Check refrigerant levels every 2-3 years
- Inspect electrical connections
- Monitor for unusual noises
Common Compressor Issues
Symptom | Possible Cause | Solution |
---|---|---|
Loud noises | Worn bearings or pistons | Professional service needed |
Short cycling | Refrigerant leak or electrical issue | System diagnostic required |
Failure to start | Capacitor or relay failure | Electrical component replacement |
For complex issues like refrigerant leaks or compressor replacement, always consult a qualified HVAC technician. The Air Conditioning, Heating and Refrigeration Institute maintains directories of certified professionals.
Choosing the Right Compressor for Your Climate
Compressor performance varies by region:
Colder Climates
Look for systems with:
- Low-temperature operation down to -22°F (-30°C)
- Two-stage or variable-speed compressors
- Enhanced vapor injection technology
Moderate Climates
Standard single-stage or scroll compressors often suffice
Hot Climates
Prioritize systems with:
- High SEER ratings (16+)
- Enhanced cooling capacity
- Corrosion-resistant components
Proper sizing is crucial – oversized compressors short cycle while undersized units run constantly. A manual J load calculation determines ideal capacity.